Fugitive Emissions
Primarily depending on the location of the process plant facility, various industry standards are used to define Fugitive Emission requirements, and criteria of acceptance while testing Control Valves.
The ISO 15848 has become one of the most adopted standards for Low Fugitive Emission Testing. The ISO 15848 is split into two different sections. Part I refers to Prototype Testing while Part II refers to Production Testing, and can usually be witnessed by end users or their third party appointed inspectors during a Factory Acceptance Test for control valve supply order.
Used by Shell and Shell affiliated companies, the “Shell MESC 77/312 – Fugitive Emission Production Testing” is extensively used as an addendum to the ISO 15848 Part II Production Testing Standard.
Another standard used for Fugitive Emission Testing is the TA-LUFT.
Originally established and implemented by the federal control of pollution in Germany the TA-LUFT became popular with the chemical industries in Europe since 2002.
The TA-Luft standard is general and approaches sealings in control valve stem with less details and consequently leaving space for interpretations.
Examples of requirements that are not fully covered by TA-luft are the thermal cycle testing for control valves.
While the TA-Luft standard briefly covers the fugitive emission criteria for control valves, it is the ISO 15848 that establishes the most number of parameters and criteria possible for the fugitive emission testing of Control Valves.
In the case of ISO 15848, for a manufacturer to claim that their control valves meet Fugitive Emission requirements, the manufacturer will have to carry out prototype testing and certification of their control valves.
These tests are specified in ISO 15848 and take into account the performance of the complete control valve and not only the packing system. This fact is explained taking into consideration that there are many packing systems available in the market specially developed for the low fugitive emission, however the standard does not only specify the requirement of leakage testing at the packing box area but also require the leak testing of the body seals
The following are the main factors that contribute to the performance of a low fugitive emission control valve:
- Packing Type
- Packing Installation Method
- Thermal Contraction factor of the packing material
- Gland Flange bolting materials & elongation factors
- Gland Flange bolting tightness torque
- Plug Stem Roughness
- Bonnet Gasket
VBG Intech’s BG series control valves are available with special options for Fugitive Emissions control.
VBG Intech has a complete range of packing types which are in compliance with the requirements of the ISO 15848 standard for differents endurances levels.
VBG Intech fugitive emission laboratory able to perform testing in-house makes the process fast and easily available for customer inspection any time.
A quick overview of ISO 15848:1 Prototype Testing’s main parameters are indicated in the tables below:
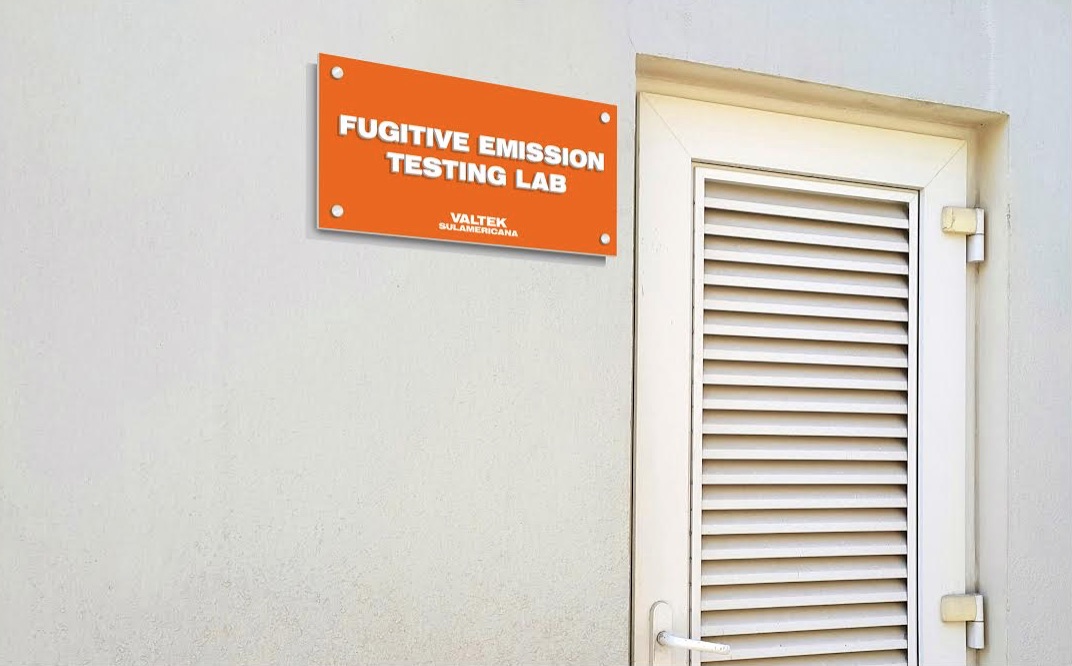
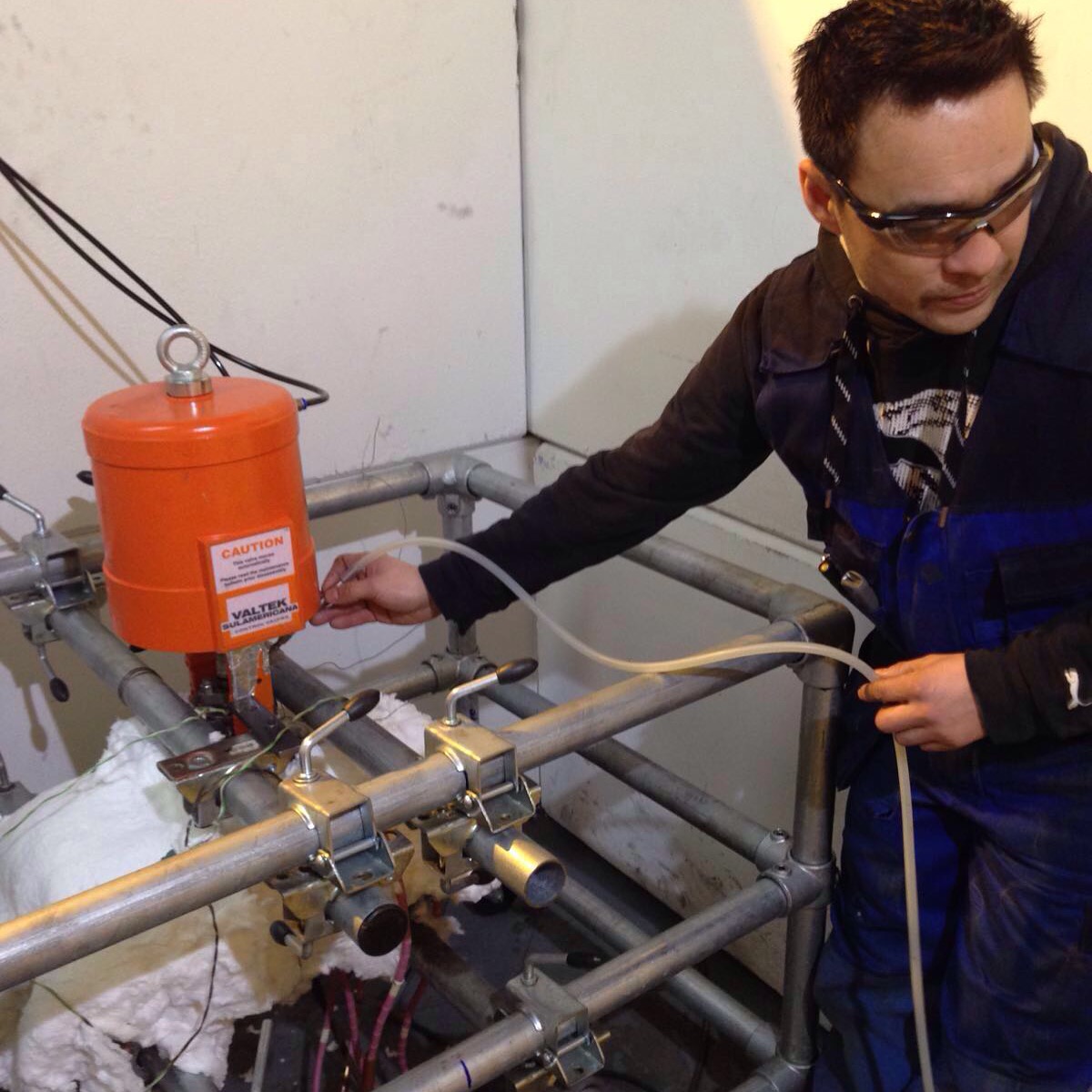
Tables below are based on information available at time of publishing this article, and may change without notice. Please refer to the latest revision of ISO 15848 for the most updated information.
Endurance Class
Classification | Cycles | Allowable Number of Tighting |
---|---|---|
CC1 | 20,000 | 1 |
CC2 | 60,000 | 2 |
CC3 | 100,000 | 3 |
Temperature Class
Classification | Valid For |
---|---|
t −196ºC | −196ºC to RT1 |
t −46ºC | −46ºC to RT1 |
t −RT1 | −29ºC to 40ºC |
t 200ºC | RT1 to 200ºC |
t 400ºC | RT1 to 400ºC |
1Room Temperature